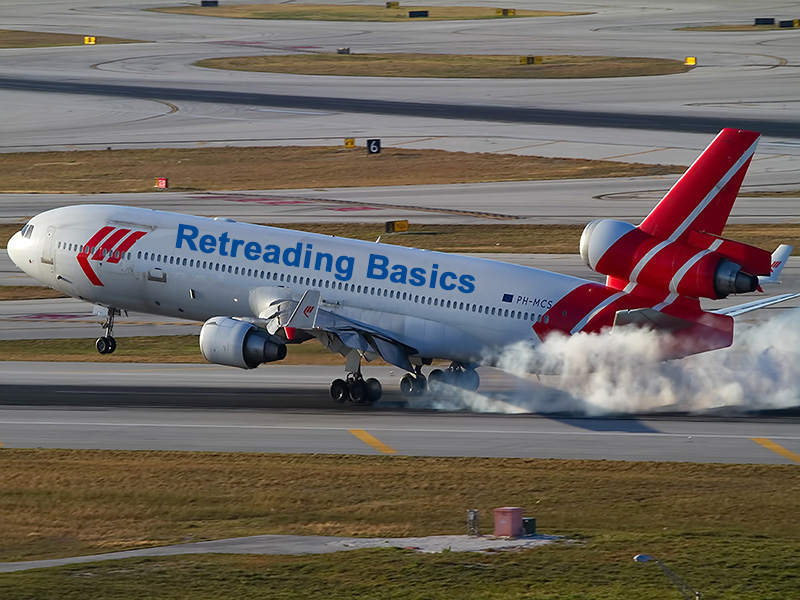
Are Retreads Safe?
Since April 2000, federal agencies have been required to use retreaded tires on their vehicles wherever practical due to Executive Order 13149. Military aircraft and all commercial airlines use retreaded tires. Nearly 80 percent of all aircraft tires in service in the US are retreads at this time.
The average retread is 270 takeoffs and landings for the life with more than 100,000 aircraft retreads in use annually. Professional retreaders adhere to stringent industry recommended practices at every step of the retreading process. In order to ensure reliable retreads are produced, most plants in North America are either franchised, licensed, consulted by or affiliated with major brand suppliers that provide technical assistance and requirements. The top retreaders in the country like Bandag are ” ISO 9001:2000 certified, so you can expect and receive consistent, quality products” which ensures consumers can track and trust the reliability of retreads.
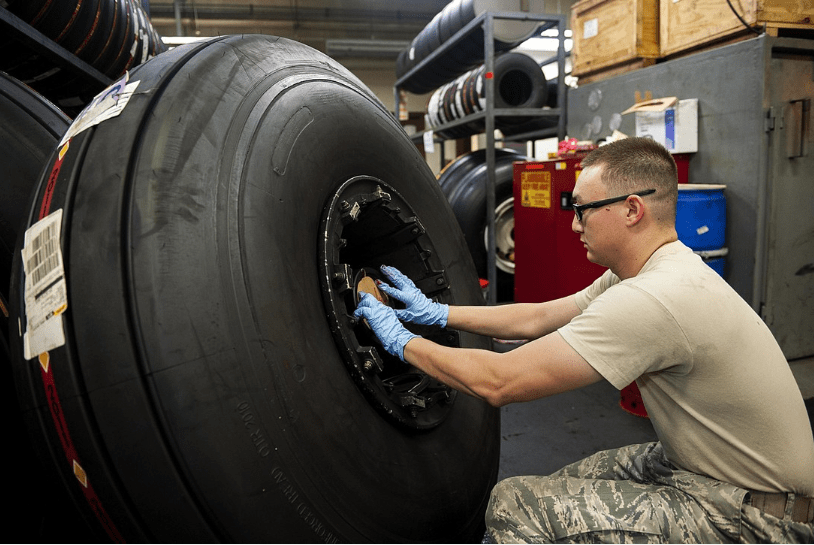
US service member adjusting tire.
Sections:
- Retreading is green
- The retread industry
- The Retread Process
- Summary and Resources
Consumers have a lot of power to ensure the industry self regulates as well. Retreaders face immediate severe financial and operational consequences if they make a mistake like contamination of a buffed surface. Retreaded tires in all applications, from passenger cars to heavy construction equipment have consistently demonstrated the same reliability in operation as new tires. Many trucking fleets plan new tire purchases to have their worn casings retreaded two or more times as a routine part of their tire budgets. Today, in North America, there are as many retreaded tires in operation as there are original tread life tires.
Retreaded tires are safely used every day on airplanes, school buses, fire engines and ambulances, trucking fleets, taxis, Postal Service vehicles, military vehicles and by millions of motorists.
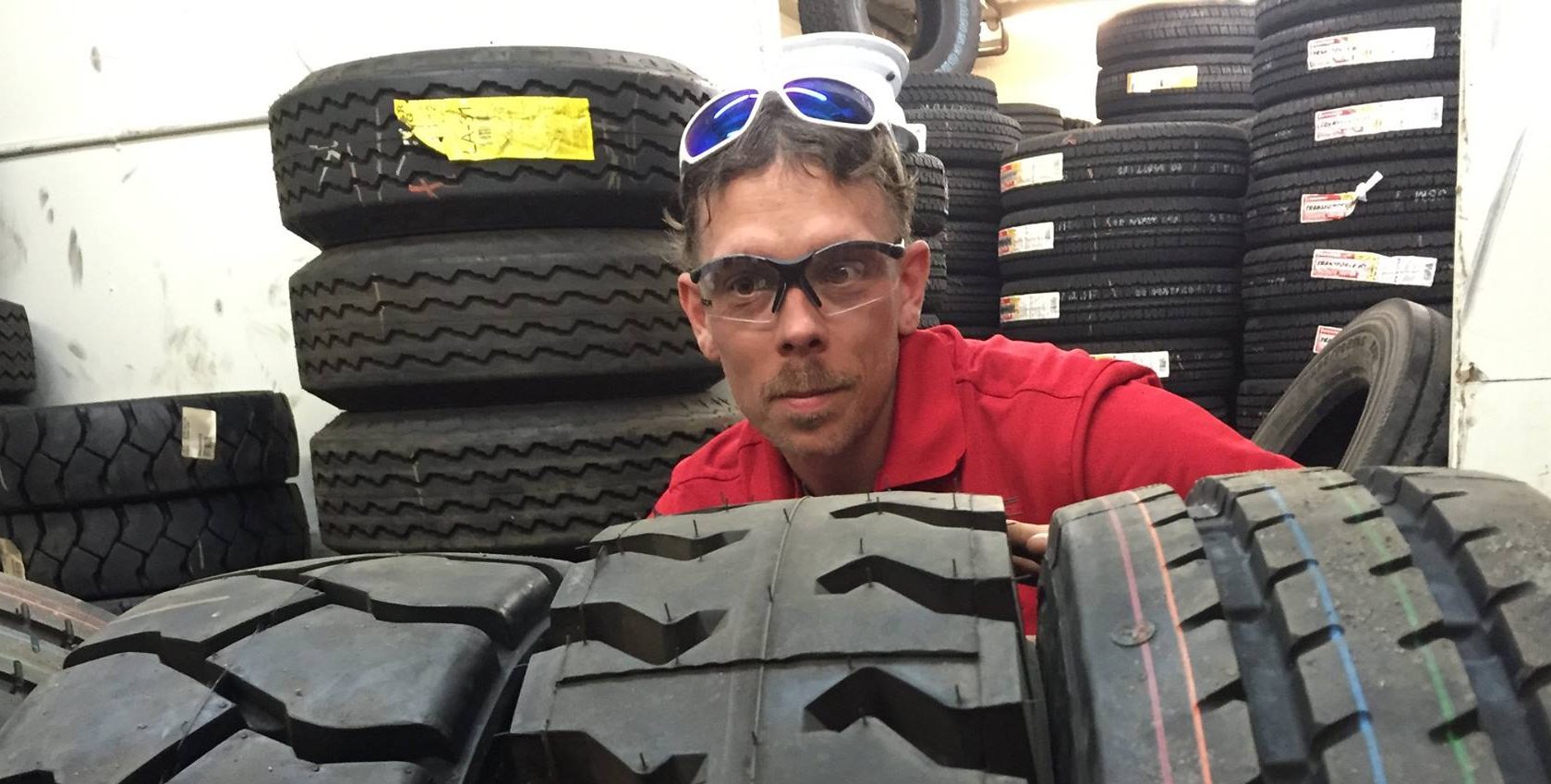
Retreading is Green!
Retreading uses less oil. New passenger tires use seven to eight gallons of oil for the rubber components of a new tires while retreading the same size tire only uses two to three gallons! Likewise, new medium truck tires required about 22 gallons versus a retread of the same size for only seven gallons.
Every year in North America, using retreads saves hundreds of millions of gallons of oil, and millions of tires continue a useful life rather than being consigned to a tire pile or landfill.
Maximize your impact! Proper tire inflation ensures the maximum life and efficiency out of your tires. This ensures they are retreadable when tread is worn and you save in fuel.
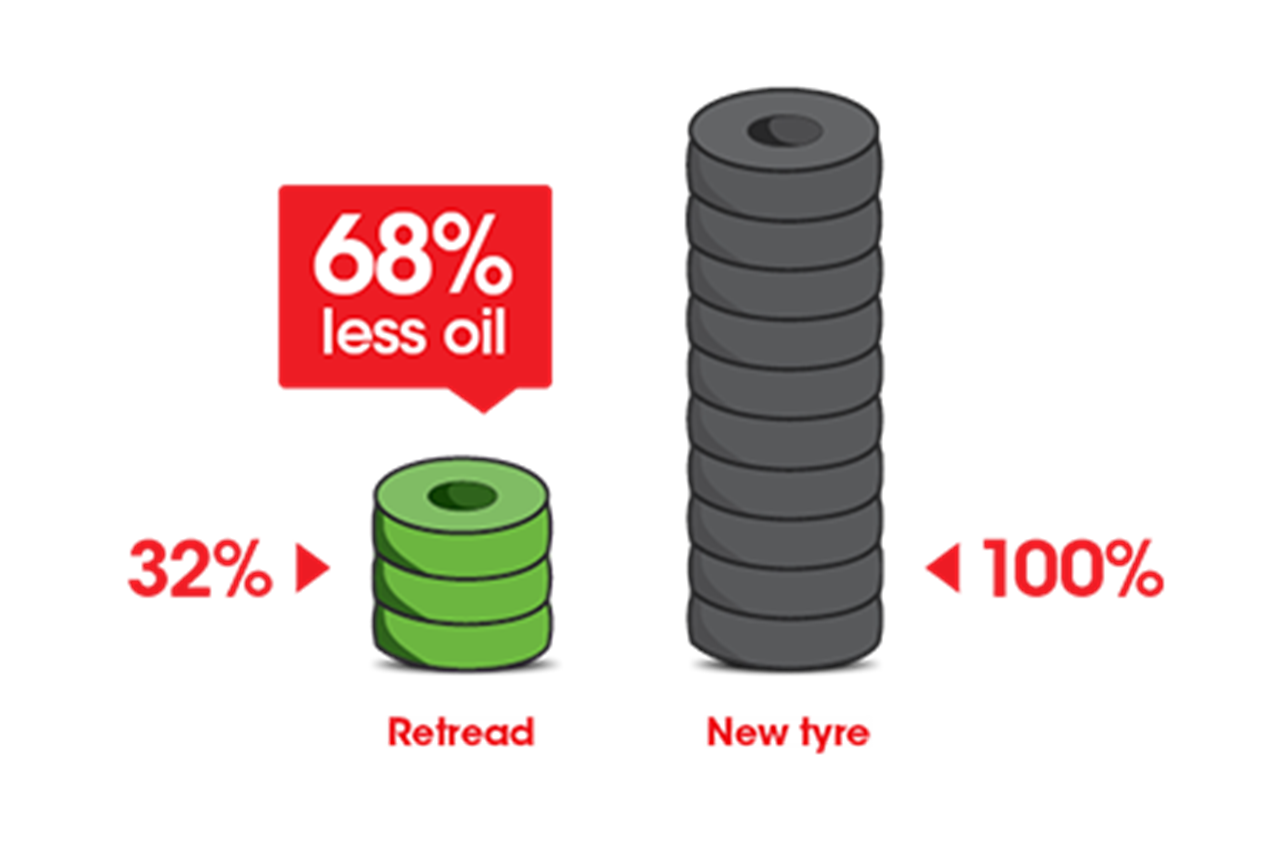
Who we are – The Retread Industry
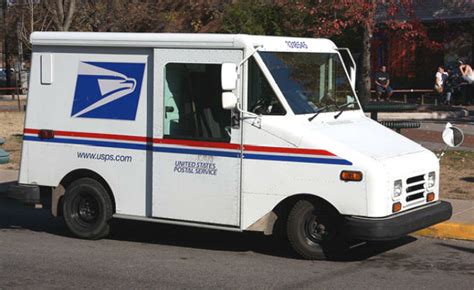
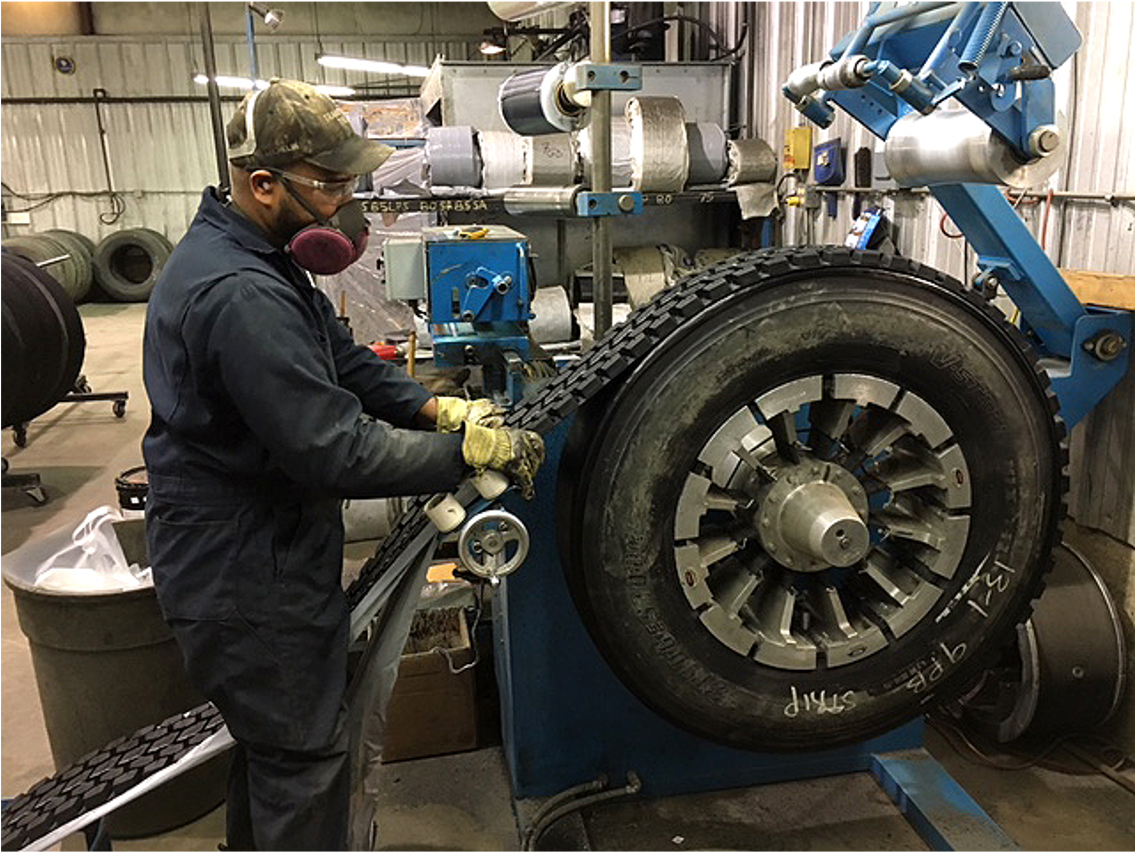
Top- USPS traditional delivery vehicle. Bottom- Tread added to a casing.
What is retreading? Retreading is where casings, worn inspected tires, receive a new tread.
Retreading uses only high quality, carefully inspected tire casings. The old-worn tread is buffed away and a new tread is bonded to the tire body in a process very similar to the manufacture of a new tire. There are a few different processing techniques, but affixing a new tread through the application of heat, time and pressure are key to the finished product.
Since the early 1900s, tire retreading has grown steadily as an established industry. The number of retread plants in North America is down to 600 independently owned and operated from 2009 numbers of approximately 850. These plants are various sizes, from small operations producing 20 retreaded tires per day to the very large plants processing 1,000 or more retreads per day. Additionally, there are plants that retread only specialized tires such as those for off-the-road, farm and construction equipment. Altogether, these plants retread millions of tires a year, using millions of pounds of synthetic and natural rubber. This represents over $3 billion in retread tires sold annually. More info on the economic impact of retreading here.
Long-haul trucking companies are a major market for retreaded tires and use millions of retread tires annually. Profitability suffers if they are unable to use retreaded tires. Radial truck tires are guaranteed by the new tire manufacturers to be retreadable in the US, however, many foreign produced tires cannot be retreaded. (In some instances, the major tire manufacturers guarantee two retreads on steel radial truck tires.)
Passenger cars, aircraft, sand and gravel trucks, delivery vans, the U.S. Postal Service (USPS), farm equipment and earthmovers can use all retreaded tires. Retreading opportunities increase throughout the US and internationally annually.
How we do it – The Retread Process
Step 1: Initial Inspection – The initial inspection determines whether a worn casing is accepted for retreading or rejected. It determines whether the tire body is technically sound enough to support another tread life and meets the customer’s specifications. Casings are rejected if they are not capable of service through another tread life.. Every operator at their position is an inspector able to reject a tire or sent back a previous step. Accepting a tire for retreading this the decision to put the company’s name on a final product and shows confidence that a person can operate a vehicle on that tire. Preliminary inspection is crucial to the success of the entire retread operation. Every operator at every post is an inspector and a tire can be rejected at any point or sent back to a previous step.
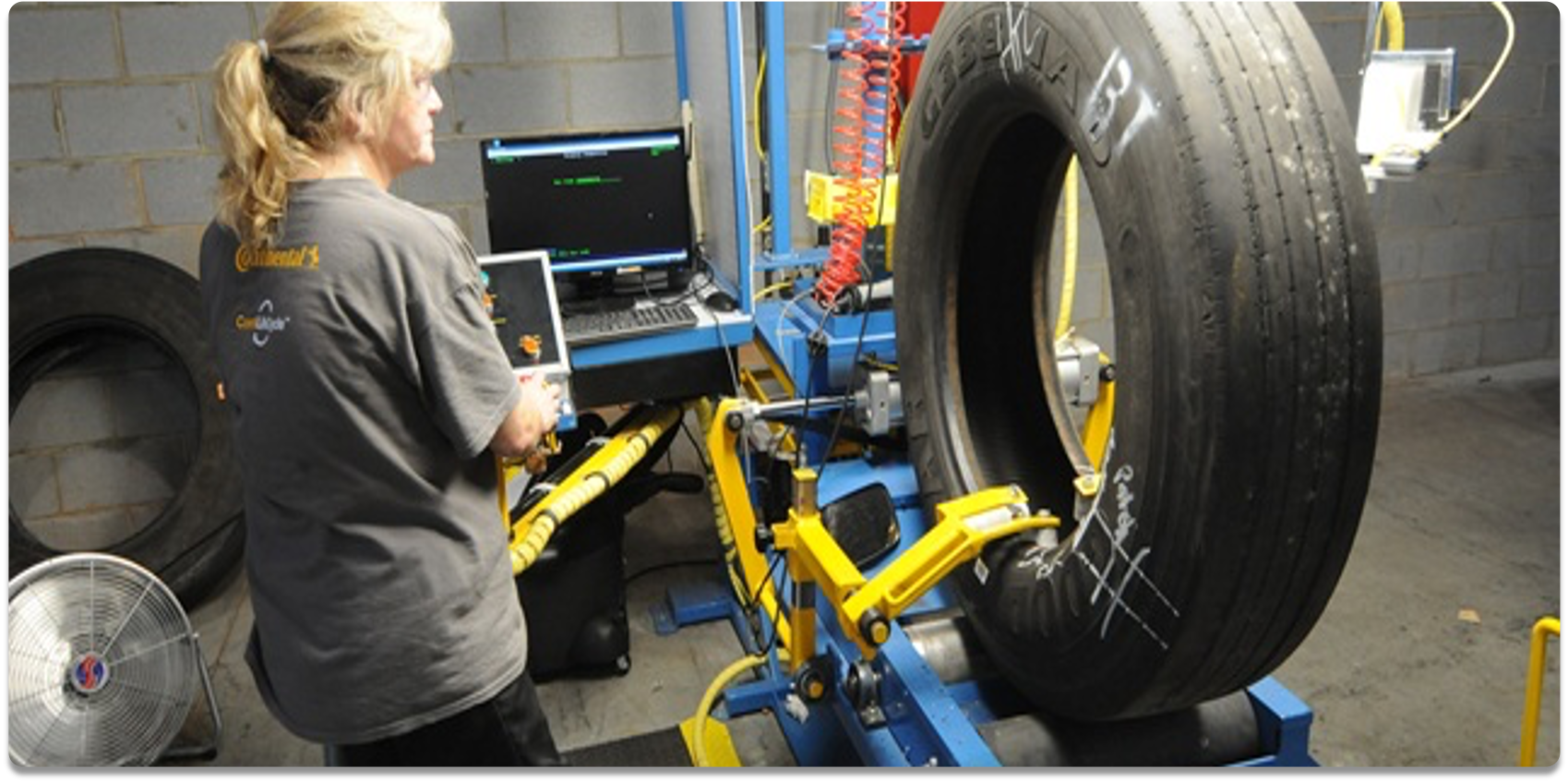
A casing goes through the testing machine looking for nail holes using 25,000 volts. Notice the markings added at the visual inspection as well.
Step 2: Non-Destructive Testing – Shearography, ultrasound, high-voltage, and X-Ray are some of the non-destructive testing methods used in retreading, enabling retreaders to actually “see through” the tire to determine if there are separations, broken steel cords or any other damage that would preclude the tire casing from undergoing another safe and useful life after retreading. Tire casings that cannot pass these tests will not be retreaded.
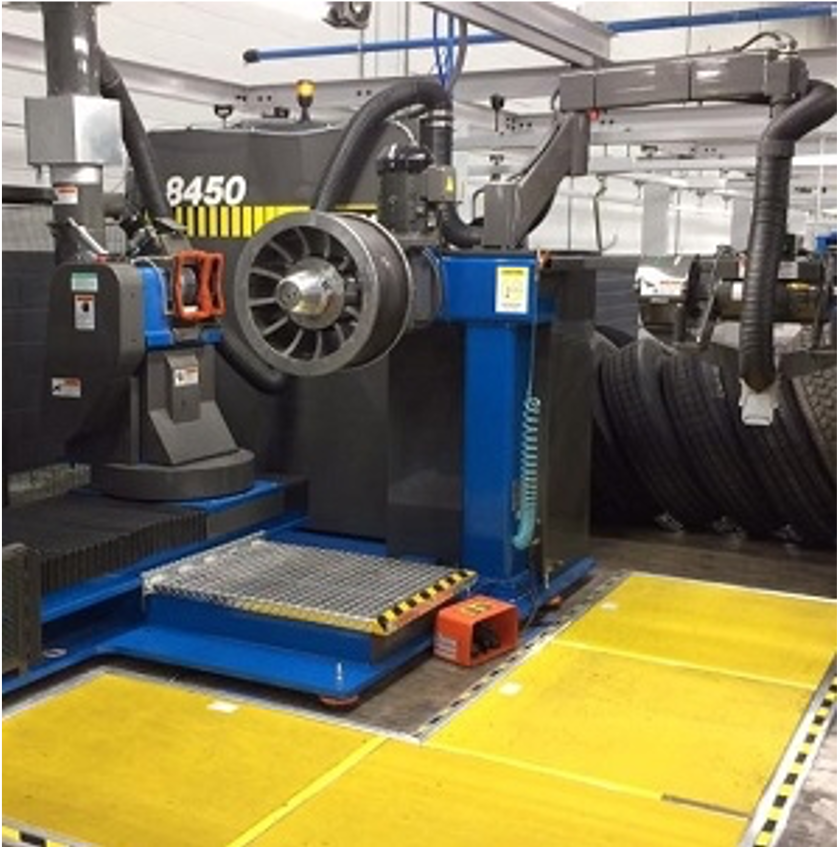
Step 3: Buffing – The worn tread is removed from a tire casing by buffing. The proper performance of the buffing operation is crucial to the retreaded tire’s future performance since this is the surface the tread is applied to.
The casing is mounted on a lathe-type machine called a buffer, and inflated. While the tire rotates, a rasp removes the remaining tread material, buffing the casing surface to the correct shape, size and texture to receive a new tread.
Every tire model has a designated crown width, profile and radius. The casing must be buffed to the particular shape that will give the best tread-to-road contact. Part of the retreaders’ expertise is the ability to buff to the exact recommended dimensions and preferred texture.
Image shows expandable hub tire is placed on before buffing process.
Step 4: Casing Preparation/Repairing – Injuries remaining in the tire casing after buffing can be repaired if the damage is within acceptable limits. Retreaders recognize which injuries can be repaired and which cannot based on TRMG, TRIB, and TIA guidelines. Where injuries are too extensive, the casing is rejected. The repair operation is a crucial step in the tire retreading process.
A properly repaired tire is intended to last the life of the new tread being applied. Repair specialists are dedicated, knowledgeable individuals who are aware of their responsibility to the end users spending time on the road using the finished product.
Step 5: Tread Application – The buffed casing is ready for a new tread after all the repairs. There are two types of vulcanizing processes that bond the tread to casings; mold cure and precure.
The Mold Cure Process – The application of tread in the mold cure retreading process is very similar to that in the new tire manufacturing process. Using one of several methods, uncured tread rubber is applied to the crown area of the buffed casing (in the case of bead-to-bead retreading, also to the sidewalls). The prepared casing, built to the correct diameter with uncured rubber material, is now ready to be placed in the mold for curing.
The Precure Process – As the name indicates, the tread rubber used in this process is molded and precured by the tread rubber manufacturer. The retreader selects the appropriate treads in strips or full circles of various designs, widths and thicknesses. In the precure retreading process, a cushion gun bonding layer is placed between the tread and casing. The proper tread width is applied to the prepared casing in a straight and even fashion. The tire then moves to the chamber for curing.
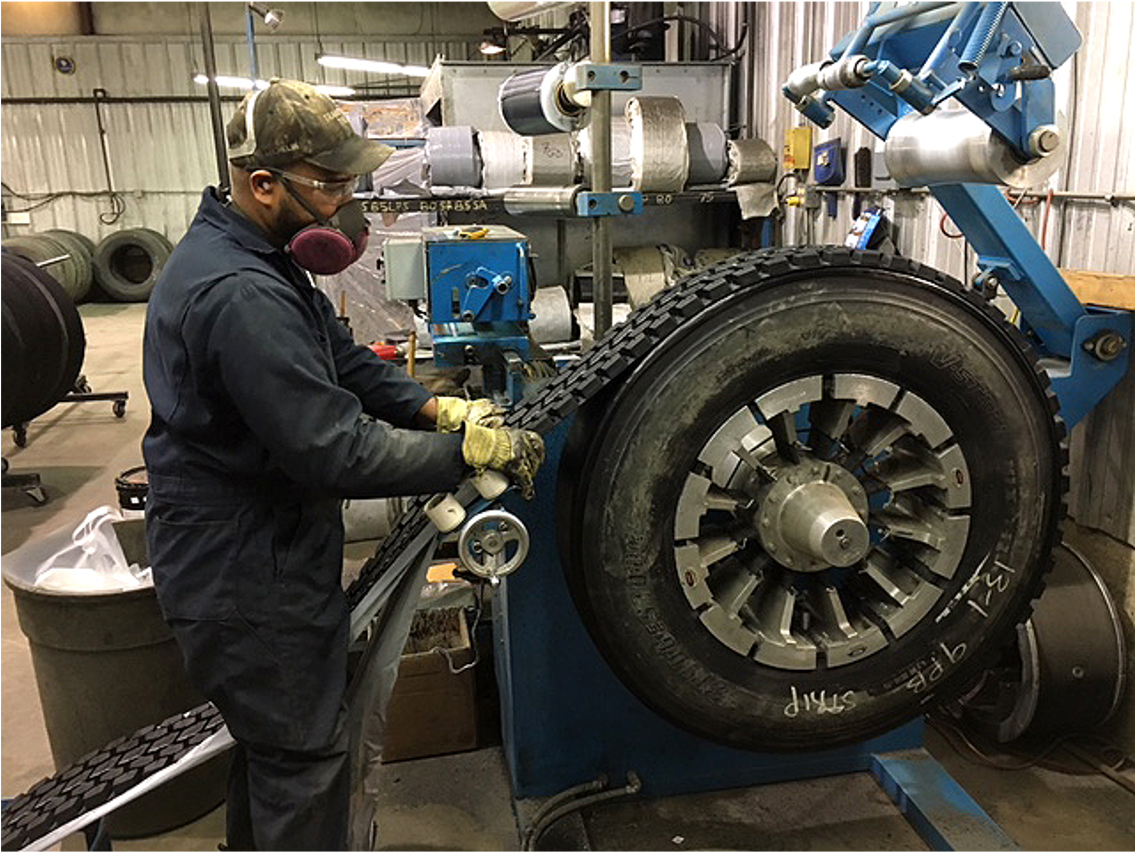
Image shows precured rubber applied to the casing. Note the ‘shiny’ layer between tread and casing that is the cushion gum between buffing surface and tread.
Step 6: Curing – Curing, or vulcanization, is the process of bonding the new tread material to he prepared tire body. During the curing process, uncured rubber transforms from a soft, tacky, stretchy substance to a tough, hard tread that resists abrasion and provides excellent mileage and traction.
In the Mold Cure Process, the prepared casing, built to the correct diameter with uncured rubber, is placed into a mold.
The tire is inflated inside the closed and heated mold and stays inflated for a time period. The casing conforms the uncured material to the mold, forming the tread design.
In the Precure Process, curing takes place within a chamber. The unit pressurizes, and the air is heated by electricity, steam or hot liquid. Once the new rubber in place, the prepared casing goes into rubber envelope or membrane much like an inner tube with a valve used to suck out the air, creating a vacuum and physical pressure on the tread. The next step is placing the tire into a chamber with specific pressure, temperature, and length of time. The tire cures with the cushion gum layer bonding the precured tread to the tire. Want tips on repairing envelopes or best practices for care?
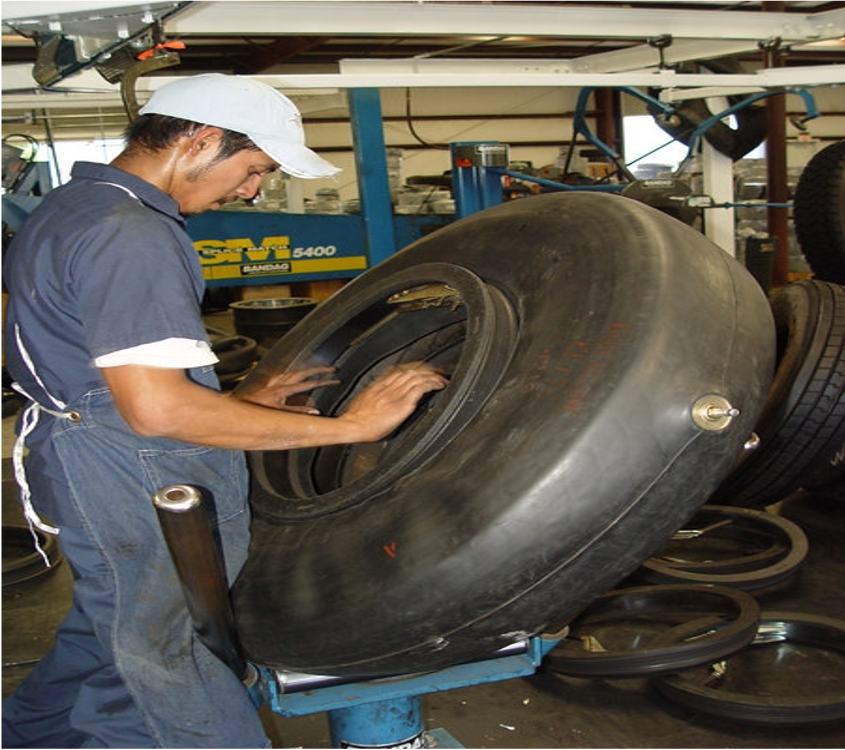
Adding flex rim to help seal envelope on the tire before loading into chamber.
Rim helps create seal on envelope over the tire to create a vacuum on the tire before heating it in the chamber seen on right.
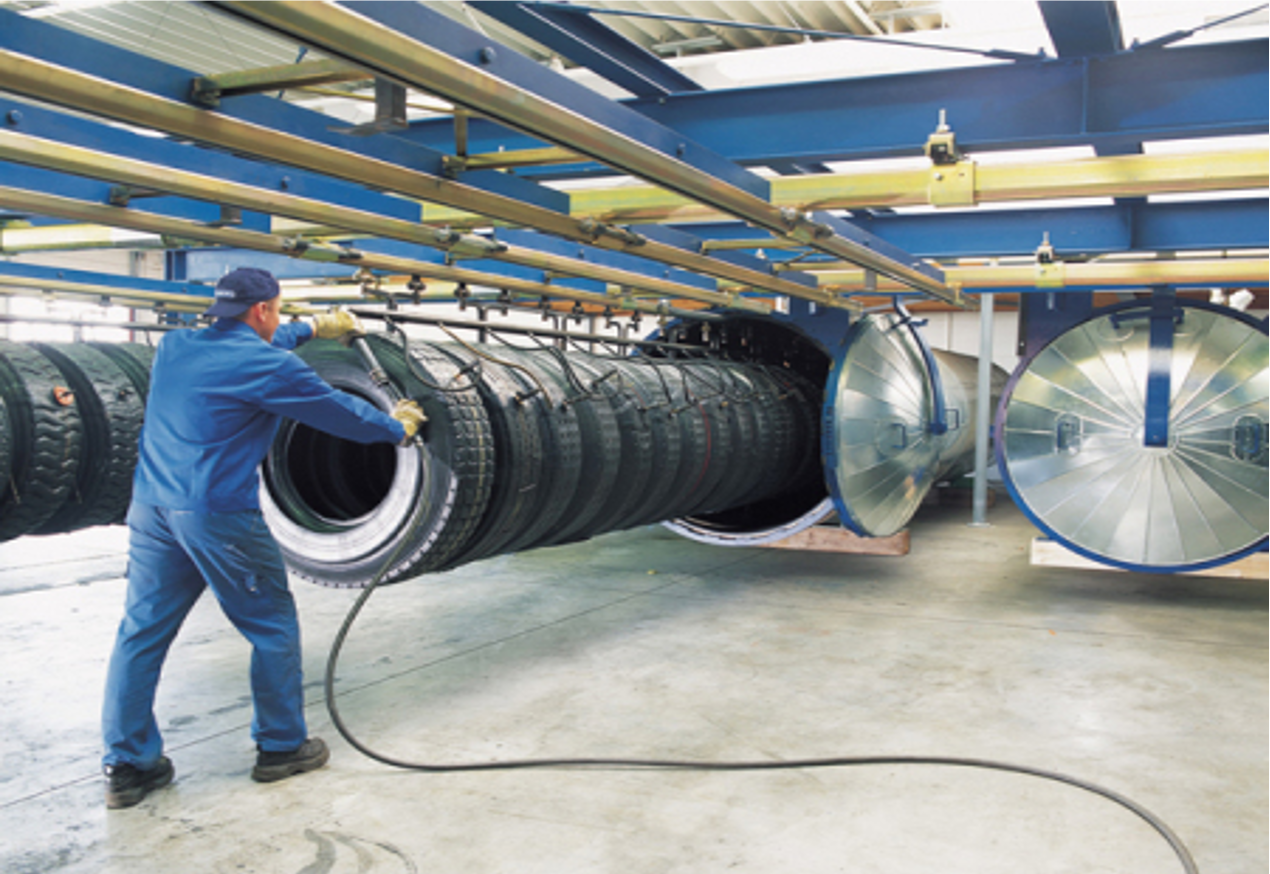
Step 7: Final Inspection – The final inspection station is the last station at the retread plant. All retreaded tires are closely inspected to ensure a reliable and attractive product for the customer. After approval, many tires are painted and labeled for a like-new appearance.
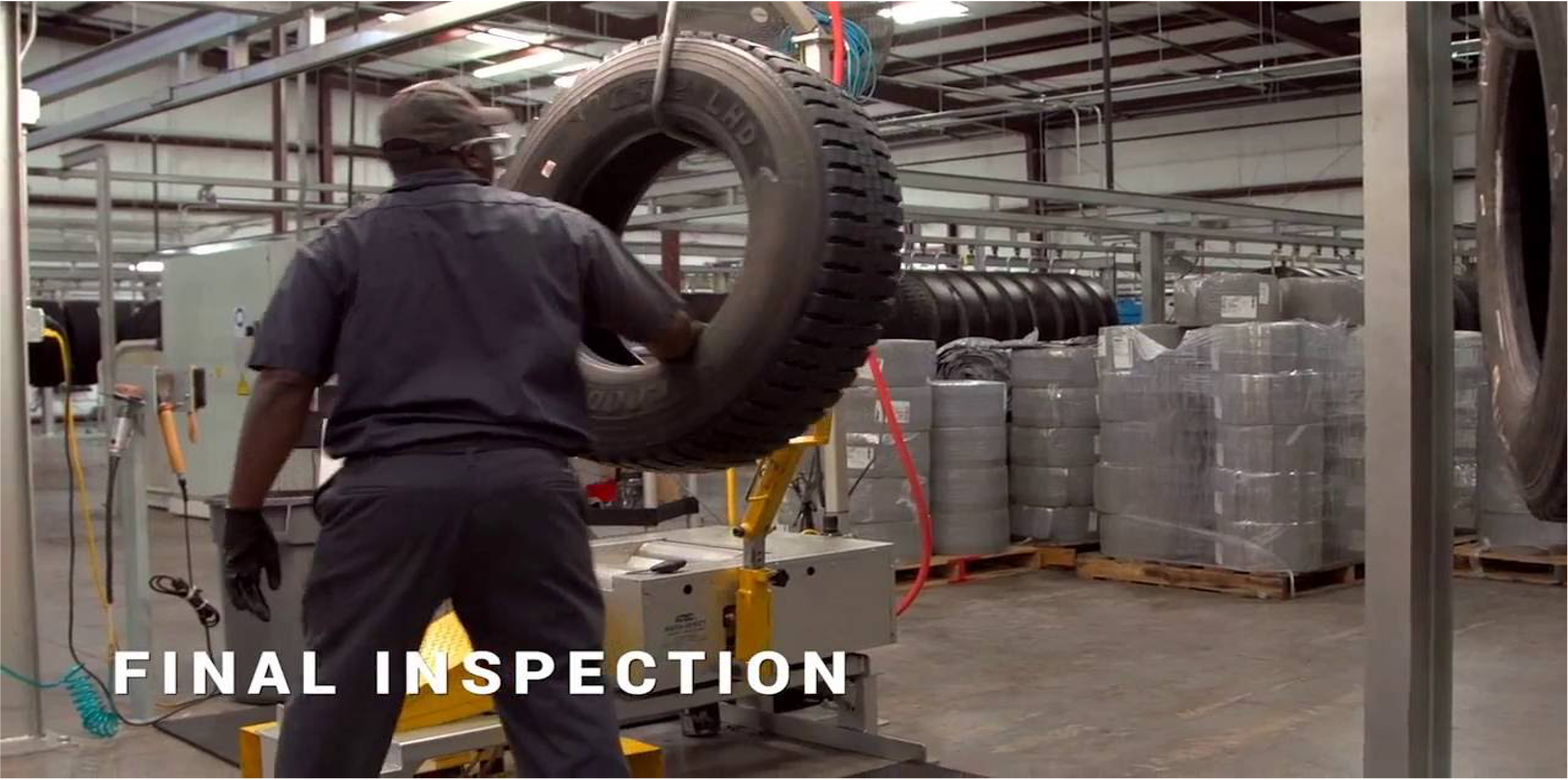
Thorough inspection at the last station.
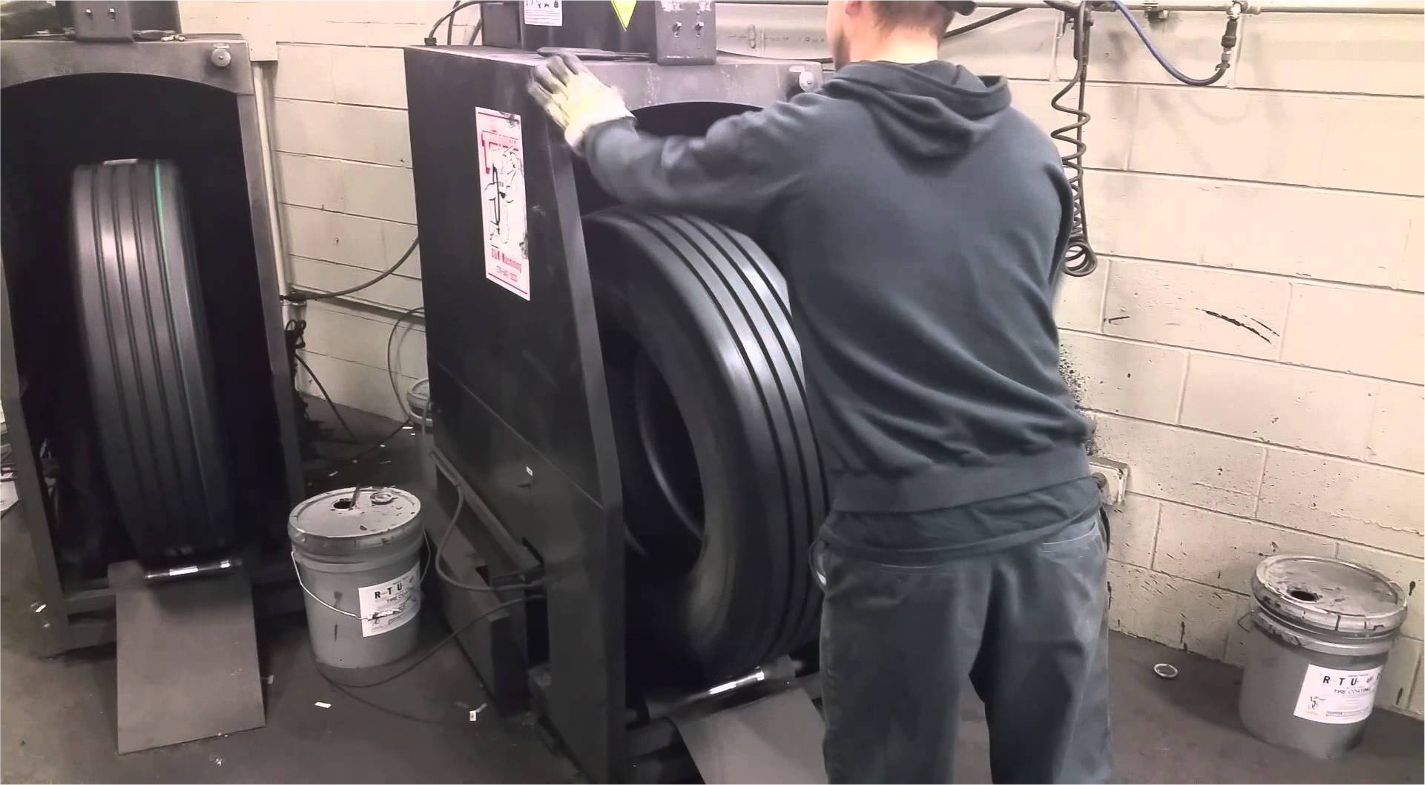
Paint machine to ensure paint stays on the tire not the shop walls!
Retread Takeaways and Resources
Retreads are produced in modern plants operated by trained professionals that adhere to strict Industry Recommended Practices at every step in the retreading process. Each retread product is traceable to the facility that produced it.
Retreaded tires are reliable. US military aircraft, commercial airlines, USPS, government vehicles, school buses, and emergency transport all use retreads. Trucking companies routinely depend on retreads for long-distance hauls. Retreaded tires are proven as reliable and durable as new tires in laboratory tests and through years of practical experience in all the same applications where new tires are used. In some cases, retreads are the product of choice for applications where new tires for a fleet. The school bus drive wheels are a prime example.
Retreading is an excellent way to save money. A properly constructed and maintained retreaded tire will give comparable miles per tread depth as a new tire. In fact, the more expensive the original new tire, the greater the retread savings. Discarding a worn tire wastes value since many tires are retreadedable one or more times. Whether you are a fleet professional, or an owner-operator, retreaded tires are a viable economic alternative to new tires.
Retreading is recycling. Because tires contain significant amounts of synthetic rubber, an oil derivative, retreading is an excellent way to conserve oil and keep tires out of landfills. Each purchase of a retreaded tire is a substantial act of conservation.
Great Resources:
- Tread Rubber and Tire Repair Materials Manufacturers’ Group TRMG
- Tire Retread & Repair Information Bureau TRIB
- Tire Industry Association TIA
- Continental
- Goodyear
- Bridgestone / Bandag
- Retreading supplies at McGeeCompany.com
- McGee Retread Catalog